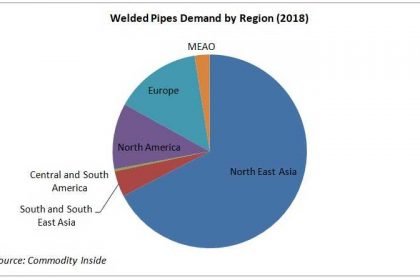
Welded pipes are produced by shaping flat steel (steel plate or steel sheet) to cylindrical shapes through mechanical pressure and then the seam is joined through welding. Quarto plate ( which is also known as reversing mill plate) is largely used in the industry for the production of welded pipes. Moreover, hot-rolled coils are also used as a substrate for the production of welded pipes and tubes. Welded pipes are also known as ERW (Electric Resistance Welded) pipe.
Types of Welded Pipes:
Spiral Welded Pipes
The weld or seam in these pipes is in the form of a spiral. Plate or sheet is shaped into spiral form through using submerged arc welding (SAW) process. These pipes are usually are in large diameters forms and mostly used as long-distance pipelines in the energy sector as well as many other sectors such as structural engineering.
Longitudinal Welded Pipes
In these pipes, the weld is made in longitudinal directions. Plates or sheets are curved and electric resistance arc welding is used in the longitudinal directions to join the seams. When a plate is of higher thickness, longitudinal submerged arc welding is also used for making such pipes.
These pipes are made after curving the steel plate in the form of pipe and performed the welding in a longitudinal direction. Mostly electric resistance welding is performed in the manufacturing of these pipes. LSAW is also used in making these pipes.
Welding Steel Pipes Types
Furnace Weld (FW) or Continuous Weld is a unique weld method to produce pipe with minimum welding defects. The process is comparatively costly. The pipe is welded by heating it in a furnace at the welding temperature followed by extrusion over a mandrel. High-performance pipes like those used in boilers are sometimes made through this process.
Submerged arc weld (SAW) is much common in the industry. The electric arc and weld are completely submerged in the fused granular flux and remain protected from oxidation during the process. In the spiral pipes, it is known as S-SAW or HSAW while in longitudinal pipes it is named as LSAW.
The most cost-effective pipe production process is through electric resistance weld (ERW). Cylindrical shaped plates or sheets are subjected to the high currents at the joining edges. The electrical resistant heat up the joint and produces weld at the seams.
Welded Pipes Finishing
The finishing of welded pipes depends on customer requirements and applications. These include threaded and coupled ends for use in long fluid transportation lines, threaded end without coupling for diverse diameter lines, Plain End or Cut Square for the general purposes. Pipes with pre-grooved or bevelled end are supplied for structural applications.
A different metallic coating like galvanising, lead lining, aluminising and claddings are also used for corrosion protection during applications. Non-metallic coatings such as oiling, paints, plastic coating, coal tar etc are also used for protection during storage and transportation. End finishing and coatings add significant costs to the welded pipes.
Designations and Specifications
ASTM A53 and API-5L are commonly used to define general specifications of welded pipes. ASTM B36.10 standard is used to define sizes and dimensions of pipes and tubes. While some of the industries have their own norms and custom sizes.
In North America, designations used to define pipes sizes are known as Nominal Pipe Size (NPS) and Schedule Number (Sch.). NPS defines the internal diameter of pipes and Sch. refers to the range of wall thickness.
In European standards, Nominal Bore (NB) is used to represent the internal diameter in mm and OD represents the outer diameters of pipes and tubes. ASTM/ANSI standard weights are usually expressed in Kg/m or lb/ft.
The following length standards are used in the market and are vital for the pipeline project designs.
1. Single random length (SRL) ranges between 18 – 25 feet plain end or 18 – 22 feet threaded and coupled pipes.
2. Double random length (DRL) ranges between 38-40 feet.
3. Longer than double random is more than 38 – 40 feet in length.
4. Cut Lengths are produced in fixed lengths within +/- 1/8 inch, while some are produced up to 80 feet long.
Top Welded Pipes and Tube Producers in the Market
- ArcelorMittal
- Condesa
- Europipe
- Evraz Group
- Handan Zhengda Steel Pipe
- Jindal SAW
- Marcegaglia
- Padana Tubi
- PSL
- Tenaris
- TMK
- United States Steel
- Welspun Power & Steel
Welded Pipe and Tube Market
Welded pipe market drivers are varied by regions. Large and medium welded pipes demand is mainly driven by major pipeline projects. Most pipeline projects have a close relationship with hydrocarbon exploration activities.
Hydrocarbon fuel demand and fuel prices are keys to the demand for welded pipes. In additions, urbanisation is also playing a key role in driving the demand which supports infrastructure for water and sewerage lines, using welded pipes. Other factors which drive welded pipes demand include GDP growth, construction, automotive and chemical industries.
Developments in the Welded Pipe Industry
North-East Asia, North America and Europe show stable demand growth in pipeline developments over the next five years. China announced in 2017 to increase its existing 112,000 km of energy pipelines network to 169,000 km by 2020 and up to 240,000 km by 2025. Japan has been planning to build a 1,500 km pipeline to import gas from Russia.
North America accounts for almost 31,000 miles of planned pipelines out of which 15,279 miles were already under construction as of 2017. One of the ongoing projects in the US is the construction of 600 miles Atlantic Coast pipeline. Nord Stream 2 project is also expected to be completed by 2021. The Middle East and Africa have 4,423 miles of pipeline projects under construction as of 2018, while 4,794 miles of pipeline projects are planned for the future.
Welded Pipes Applications
Pipes are used for shipping oil and gas from oil fields to export terminals, refineries and end-users. The global pipeline transportation industry is driven by increasing global energy demand and fuel trade.
Welded steel pipes are also used in construction and infrastructure sectors for different applications. These applications include scaffoldings, electrical and light poles, structural columns and beams in steel structure buildings like stadium roofs, metro and railway stations. These pipes can also be used in the sewage line and water supply lines.
The chemical industry is also one of the major consumers of welded steel pipes. Steel pipes are used to construct chemical processing lines, industrial sheds, and mechanical structures. Some of the sub-sectors include petrochemicals, agrochemicals, construction chemical, resins and polymers, synthetic foods processing plants, electronic chemicals, gas manufacturing, cement plants, pesticides manufacture, fertilizers industry, pharmaceutical industry and acid manufactures etc.
Welded steel pipes are also used in the automotive industry in making body frames supporting column and structures. These pipes and tubes are also used in engine exhausts.
Other end-user sectors include the mechanical sector, industrial sector, shipbuilding, energy and power sectors and metal furniture. In the mechanical industry, welded tubes find their applications in mechanical structures of machines, rollers of conveyor belts or in other cylindrical structures like hydraulic lifts, mills, production lines etc.
About Commodity Inside Tube and Pipes Capabilities:
Commodity Inside has a vast experience in the steel pipes and tubes market. We have a number of off the shelf reports on the pipe and tube industry. We also provide consulting and bespoke studies. Our initial scoping assessment is free of costs. Please contact us now about your query at Research@commodityinside.com