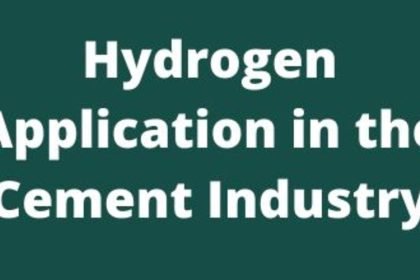
The cement industry is one of the largest emitters of carbon dioxide (CO2) globally, accounting for over 7% of total CO2 emissions. As countries aim to meet their climate goals under the Paris Agreement, there is growing pressure on industries to decarbonize. Hydrogen, with its zero-emissions profile, has emerged as a promising pathway for decarbonization in the cement industry.
Hydrogen can be produced from a range of feedstocks, including natural gas, biomass, and water. In the cement industry, green hydrogen, which is produced from water using renewable energy sources such as solar or wind, is the most promising option for decarbonization.
Green hydrogen can be produced using a process called electrolysis, which involves splitting water into its constituent parts, hydrogen and oxygen, using electricity. The hydrogen can then be stored and transported for use in the cement industry.
There are several ways in which hydrogen can be used in the cement industry to reduce emissions. These include:
- Fuel switching: Hydrogen can be used as a fuel in the cement production process, replacing fossil fuels such as coal and natural gas. This can significantly reduce CO2 emissions, as hydrogen combustion produces only water vapor and no CO2.
- Clinker reduction: Clinker, a key ingredient in cement production, is responsible for a significant portion of CO2 emissions in the industry. Hydrogen can be used to reduce the amount of clinker needed in cement production, as it can be used as a reducing agent in the raw material mix. This can help reduce CO2 emissions by up to 50%.
- Carbon capture and utilization: Hydrogen can be used to capture and utilize CO2 emissions from cement production. Carbon capture and utilization involve capturing CO2 emissions and using them as feedstock for the production of other products, such as building materials or fuels.
While hydrogen offers a promising pathway to decarbonization in the cement industry, there are several challenges that need to be addressed. These include:
- Cost: Green hydrogen is currently more expensive to produce than fossil fuel-based hydrogen. However, as renewable energy costs continue to decline, the cost of green hydrogen is expected to fall.
- Infrastructure: The current infrastructure for hydrogen production, storage, and transportation is not sufficient for large-scale use in the cement industry. Significant investment is needed to develop the necessary infrastructure.
- Safety: Hydrogen is highly flammable and requires careful handling and storage. Adequate safety measures need to be put in place to ensure that hydrogen use in the cement industry is safe.
Despite these challenges, there are several opportunities for hydrogen in the cement industry. These include:
- Climate benefits: Hydrogen use in the cement industry can significantly reduce CO2 emissions, helping countries meet their climate goals under the Paris Agreement.
- Energy security: The use of hydrogen in the cement industry can help reduce dependence on fossil fuels and increase energy security.
- Job creation: The development of a hydrogen economy in the cement industry has the potential to create new jobs in areas such as research and development, manufacturing, and infrastructure development.
The cement industry is a significant contributor to global CO2 emissions, and there is an urgent need for decarbonization. Hydrogen, with its zero-emissions profile, offers a promising pathway for decarbonization in the industry. While there are several challenges that need to be addressed, the opportunities presented by hydrogen use in the cement industry are significant, and the development of a hydrogen economy has the potential to create a more sustainable future for the industry.